Shell Mill Cutter
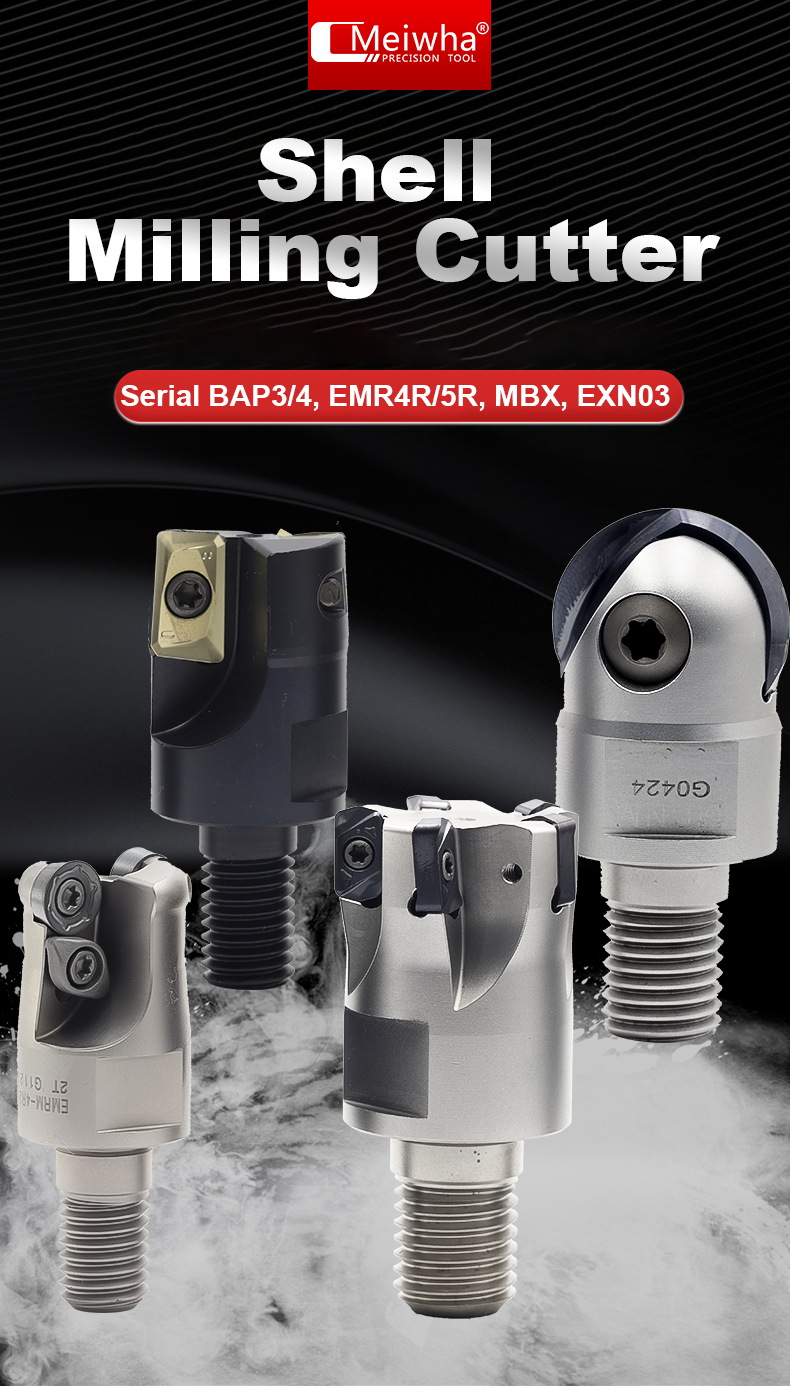
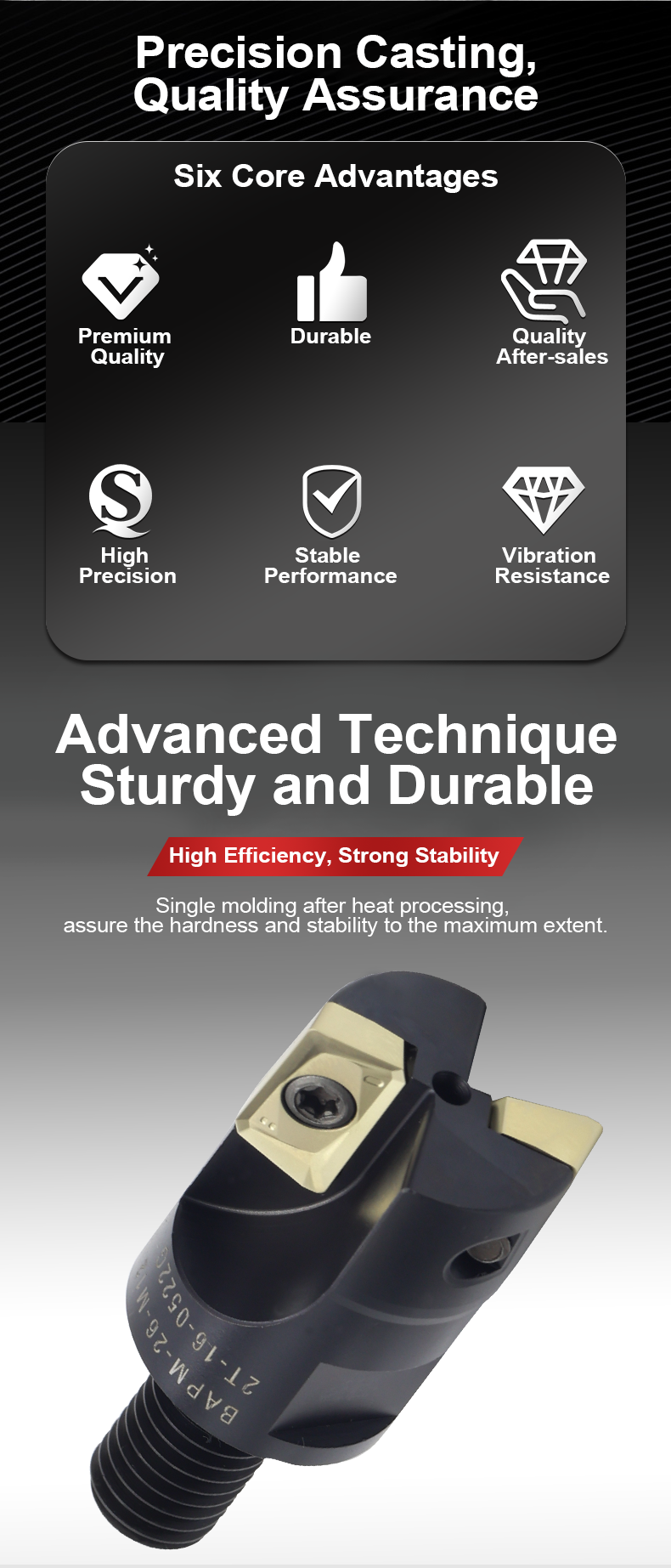
When Use Shell Mill?
A Shell Mill is often used in the following situations:
Large Surface Milling: Shell mills have larger diameters, making them ideal for milling large surface areas quickly.
High Productivity: Their design allows for more inserts and higher feed rates, improving productivity.
Versatility: The tooling can be easily changed, making shell mills versatile for different materials and finishes.
Better Surface Finish: The increased number of cutting edges often leads to a smoother finished surface.
Cost-Effectiveness: Despite higher initial costs, the ability to replace individual inserts rather than the entire tool can save costs in the long run.
Shell Mill Advantages
Versatility – Shell mills can perform almost any type of peripheral or slot milling operations. Their flexibility allows one tool to mill flat surfaces, shoulders, slots, and profiles. This can reduce the number of tools required in the shop.
Material Removal Rate – The large cutting surface of shell mills means they can remove material faster than end mills. Their high metal removal rates make them well-suited for roughing cuts and heavy machining applications.
Stable Cutting – The broad cutting edges and rigidity of shell mill bodies provides stable cutting, even with deep axial depths of cut. Shell mills can take heavier cuts without deflection or chatter.
Chip Control – The flutes in shell mill cutters provide efficient chip evacuation even when milling deep cavities or pockets. This allows them to mill cleaner with less chance of chip recutting.
Disadvanatages of Shell Mill:
Limited Application: Like face mills, shell mills are primarily used for face milling and may not be suitable for detailed or complex milling operations.
Cost: Shell mills can also have a higher initial cost due to their size and complexity.
Requires Arbor: Shell mills require an arbor for mounting, which adds to the overall cost and setup time.
Elements of Shell Mill Tool Selection
Cutter Material – Carbide shell mills offer the best wear resistance for most materials. High speed steel can also be used but is limited to lower hardness materials.
Number of Teeth – More teeth will provide a finer finish but lower feed rates. 4-6 teeth is common for roughing while 7+ teeth are used for semi-finishing/finishing.
Helix Angle – A lower helix angle (15-30 degrees) is recommended for difficult to machine materials and interrupted cuts. Higher helix angles (35-45 degrees) perform better in general milling of steel and aluminum.
Flute Count – Shell mills with more flutes allow higher feed rates but sacrifice space for chip evacuation. 4-5 flutes is most common.
Inserts vs Solid Carbide – Inserted tooth cutters allow indexing of the replaceable cutting inserts. Solid carbide tools require grinding/sharpening when worn.
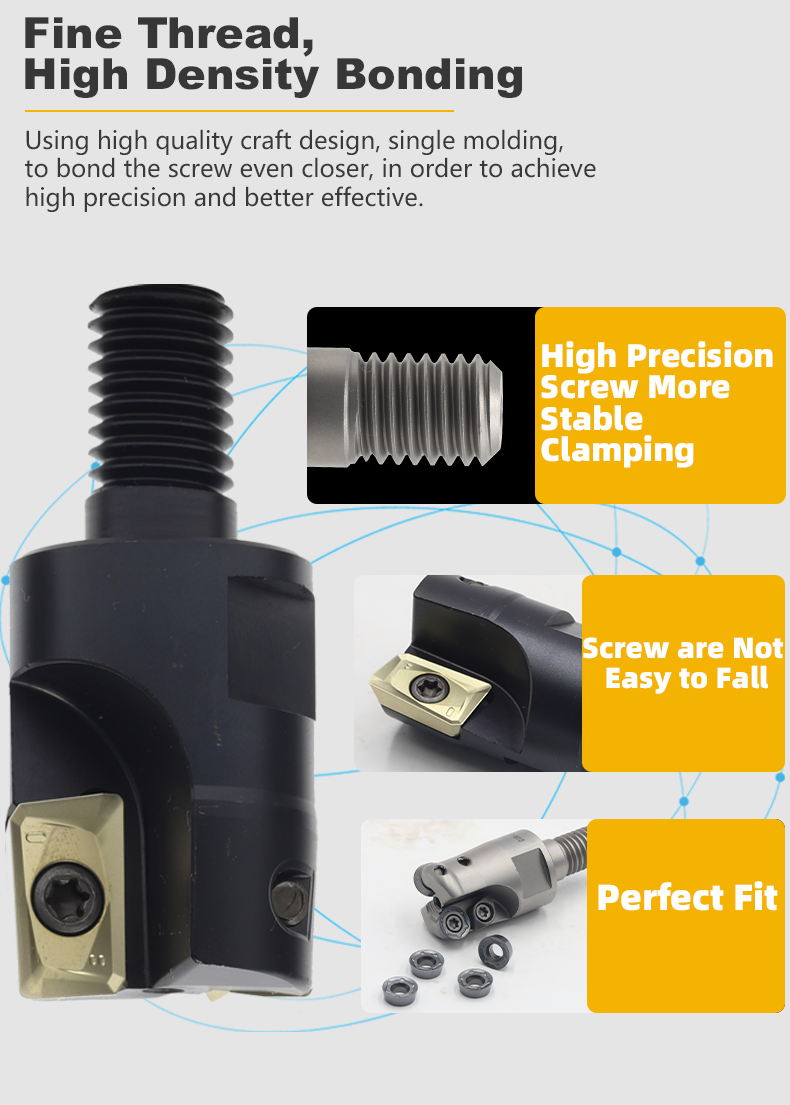
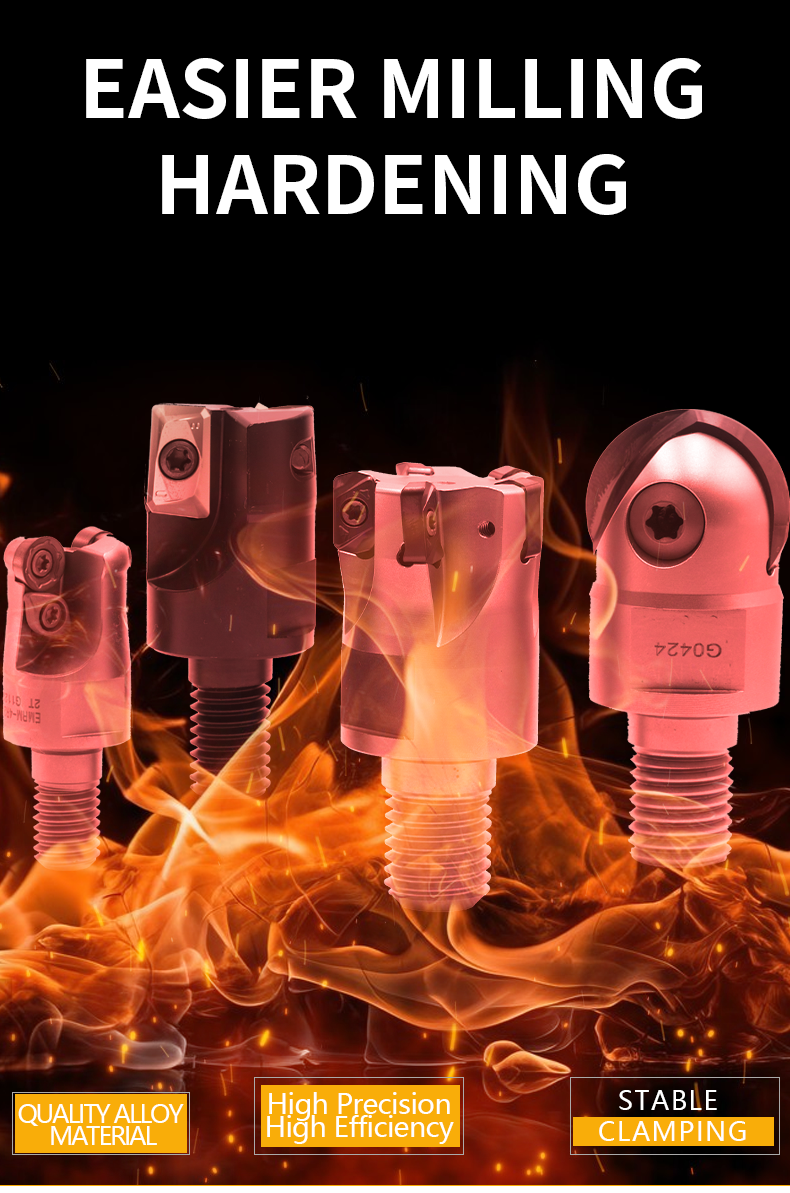
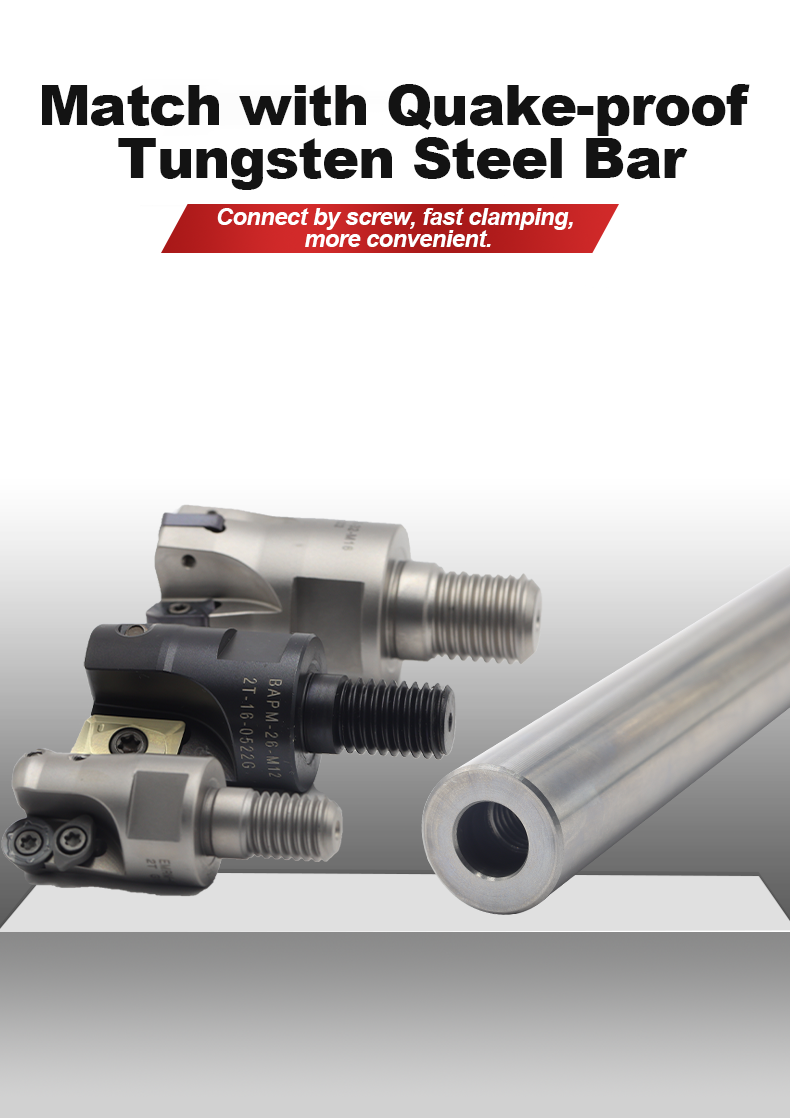
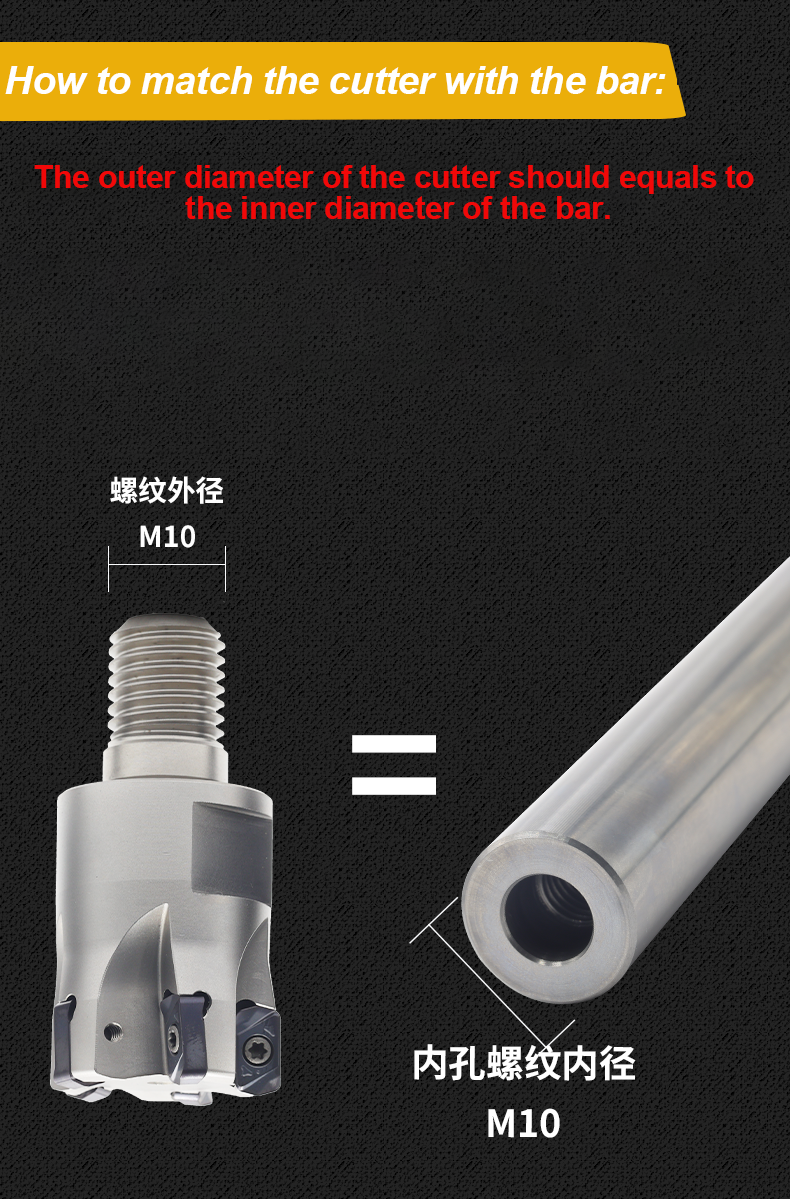
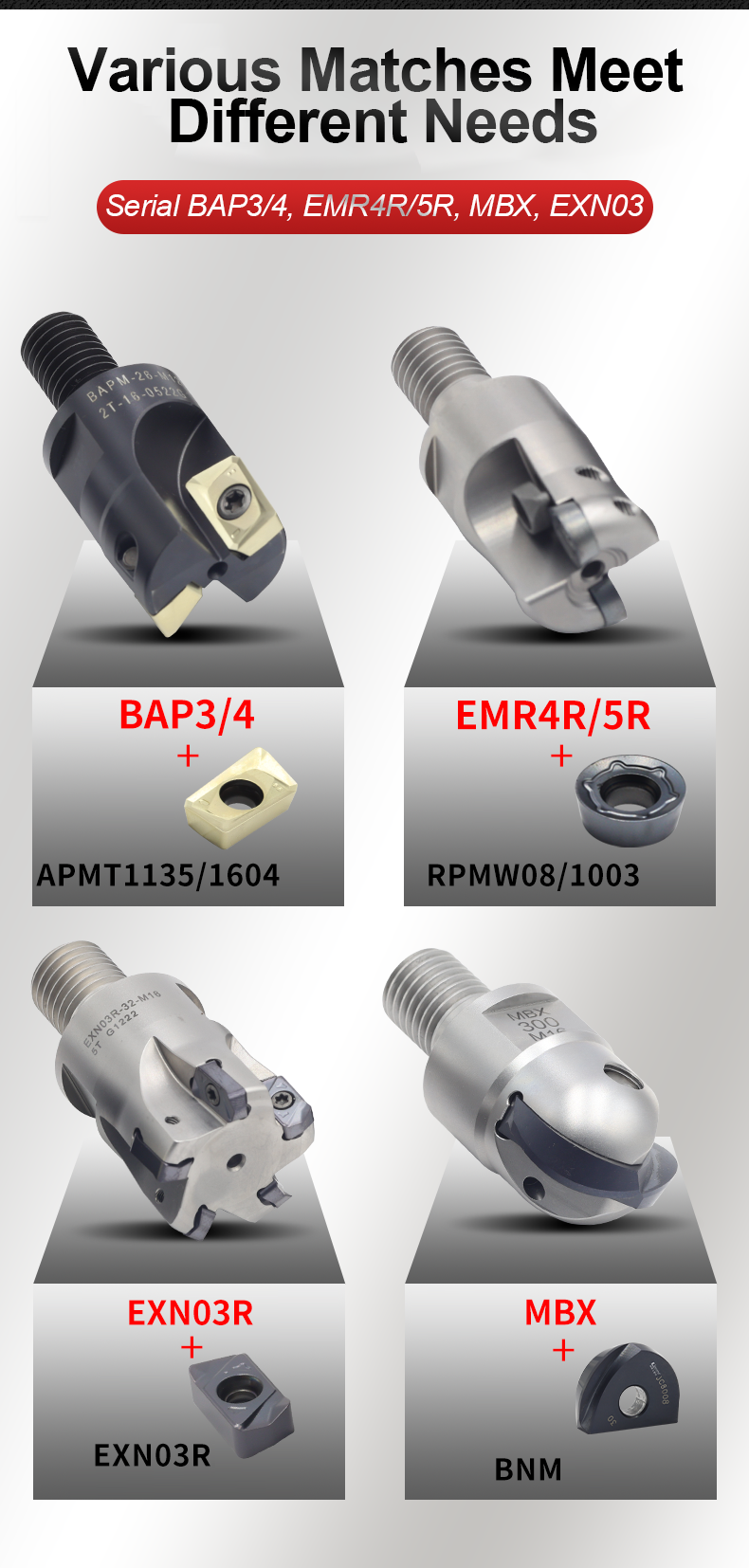